Think BIG
Siemens und die Bundesimmobiliengesellschaft BIG können auf zahlreiche gemeinsame Projekte zurückblicken.
Digitale
Transformation
Transformation
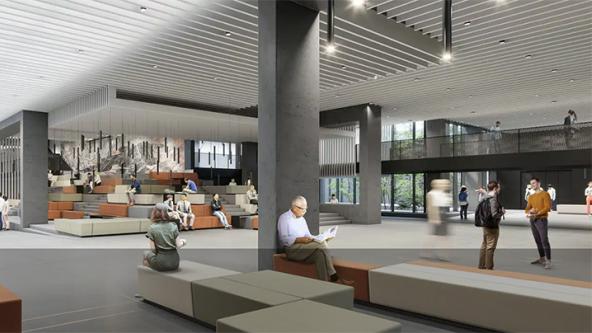
Technikerinnen im Dialog
Erstes Female Tech Community-Treffen in der Siemens City in Wien.
Empowered
People
People
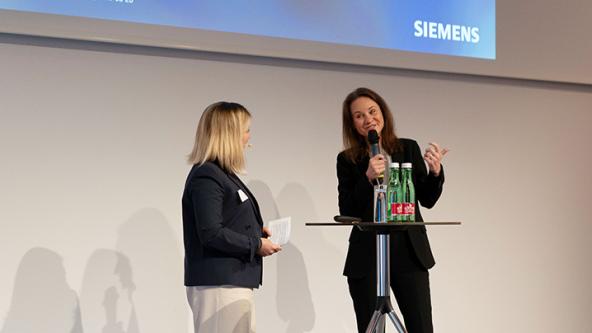
„Energierevolution jetzt!“
Fachvorträge, inspirierende Keynote und Top-Technik bei der SI EA Fachtagung „Spannung in Salzburg 2025“.
Digitale
Transformation
Transformation
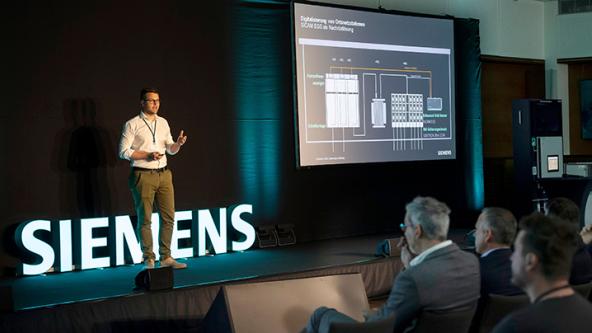
Bessere Batterien
Siemens als Technologiepartner: Hirano steigert Qualität und Performance in der Batterieherstellung.
Digitale
Transformation
Transformation
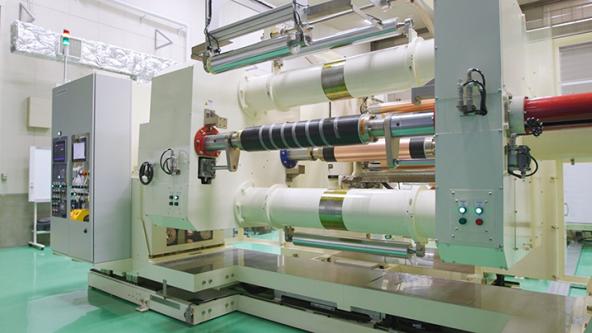
Nachhaltigere Entscheidungen treffen
Umwelt &
Nachhaltigkeit
Nachhaltigkeit
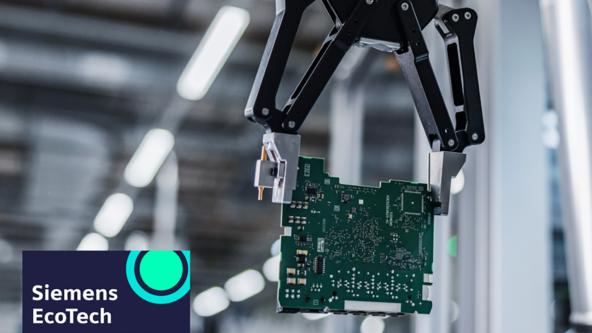
„Überzeugt von Vielfalt und Diversität“
Das OVE FEM-Netzwerktreffen in der Siemens City.
Empowered
People
People
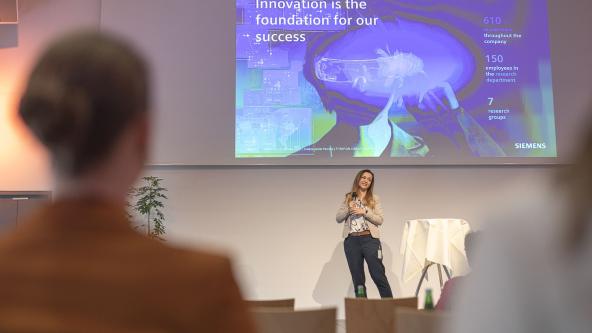
Österreich radelt zur Arbeit
Fit zum Job und Chance auf Preise sichern.
Empowered
People
People
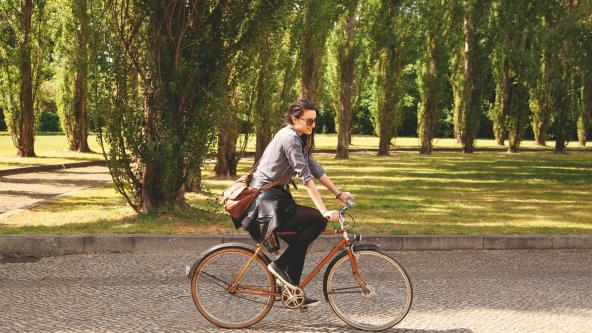
Umweltfreundliche Energieversorgung
Neue F-Gas-freie Mittelspannungsschaltanlage für die Energienetze Steiermark.
Umwelt &
Nachhaltigkeit
Nachhaltigkeit
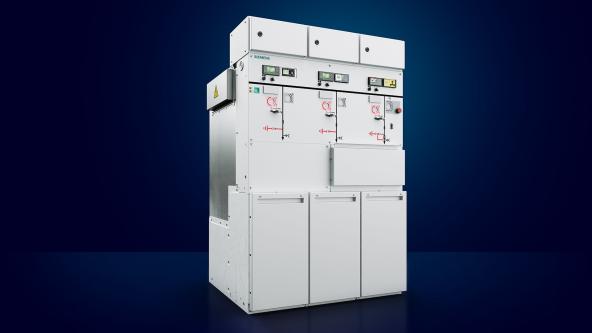
„Führung ist kollaborativer geworden“
CEO Patricia Neumann in der Tageszeitung "Die Presse".
Empowered
People
People

Auf Nummer sicher
Cybersecurity-Workshop in Wien
Digitale
Transformation
Transformation
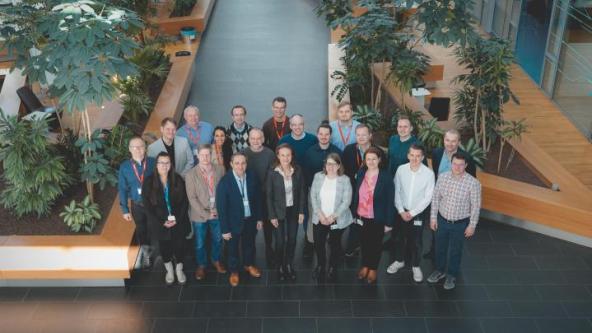
Wenn Glas immer grüner wird
Strategieplan der Stoelzle Glasgruppe für die Senkung des Energieverbrauchs um 20 Prozent und halber CO2-Ausstoß bis 2030
Umwelt &
Nachhaltigkeit
Nachhaltigkeit
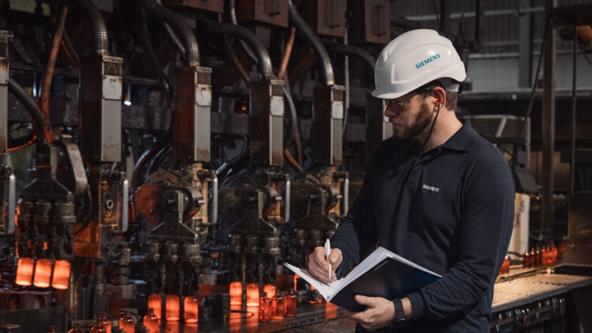
Partner von der Pike auf
Siemens als Gründungsmitglied beim Fest zum 50jährigen Bestehen des VSÖ.
Corporate
Citizenship
Citizenship
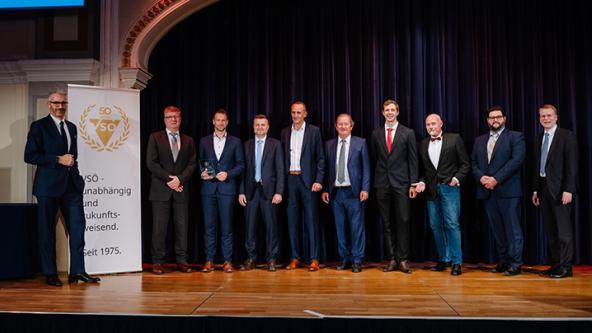
Auf den Flügeln des Erfolgs
WIKARUS: Österreich auf Platz 2 in der Kategorie "Unternehmen des Jahres" beim Salzburger Wirtschaftspreis.
Corporate
Citizenship
Citizenship
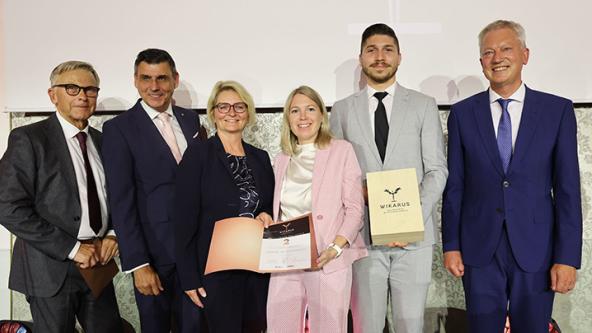
Produktion auf nächstem Level
„Accelerate your digital Transformation“: Siemens auf der SMART Automation 2025.
Digitale
Transformation
Transformation
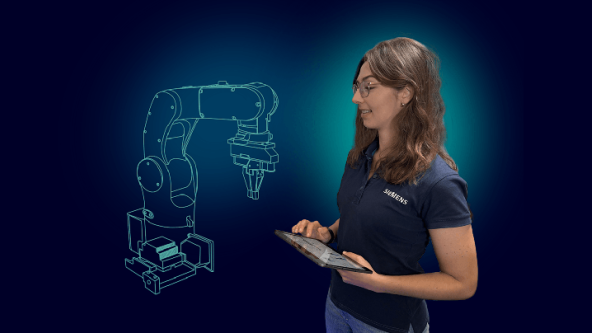
Lebenswichtiges Trinkwasser
Nachhaltigkeitsprojekt „Shoaiba 5“ zur Meerwasserentsalzung abgeschlossen.
Umwelt &
Nachhaltigkeit
Nachhaltigkeit
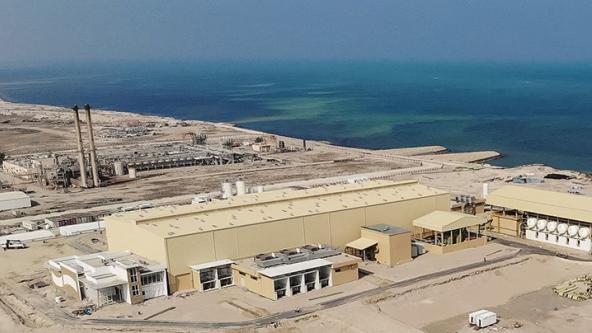