Think BIG
Siemens und die Bundesimmobiliengesellschaft BIG können auf zahlreiche gemeinsame Projekte zurückblicken.
Digitale
Transformation
Transformation
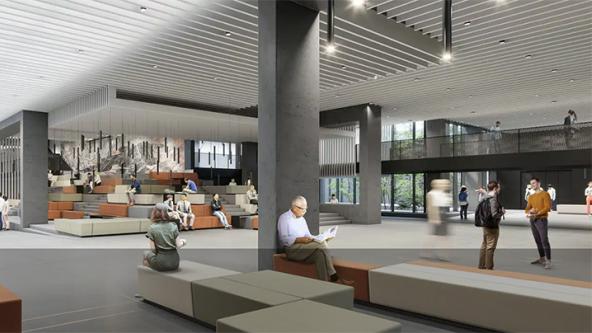
Technikerinnen im Dialog
Erstes Female Tech Community-Treffen in der Siemens City in Wien.
Empowered
People
People
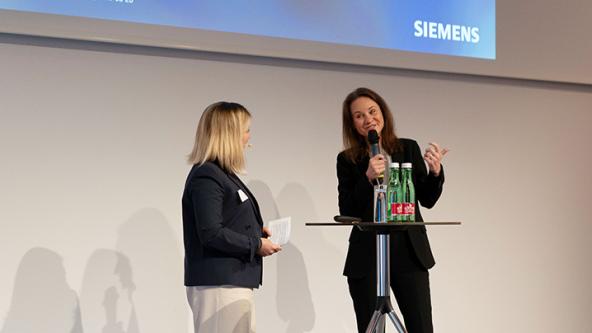
„Energierevolution jetzt!“
Fachvorträge, inspirierende Keynote und Top-Technik bei der SI EA Fachtagung „Spannung in Salzburg 2025“.
Digitale
Transformation
Transformation
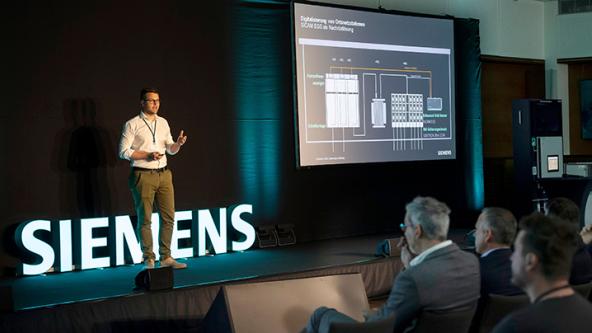
Bessere Batterien
Siemens als Technologiepartner: Hirano steigert Qualität und Performance in der Batterieherstellung.
Digitale
Transformation
Transformation
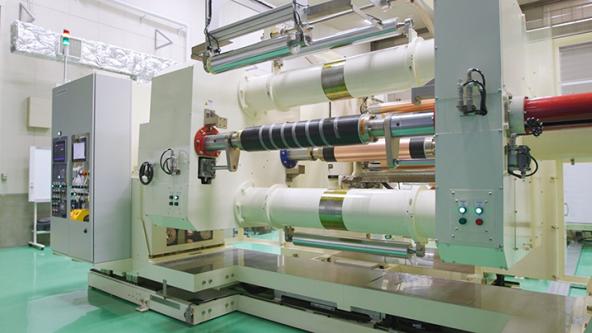
Nachhaltigere Entscheidungen treffen
Umwelt &
Nachhaltigkeit
Nachhaltigkeit
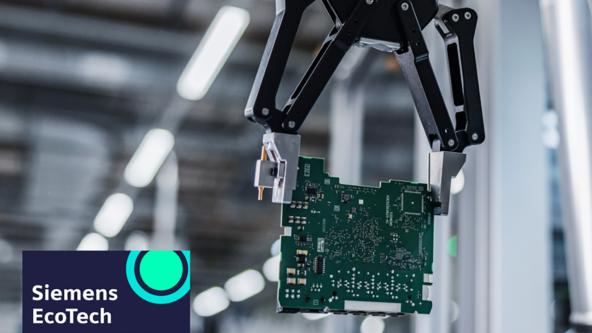
„Überzeugt von Vielfalt und Diversität“
Das OVE FEM-Netzwerktreffen in der Siemens City.
Empowered
People
People
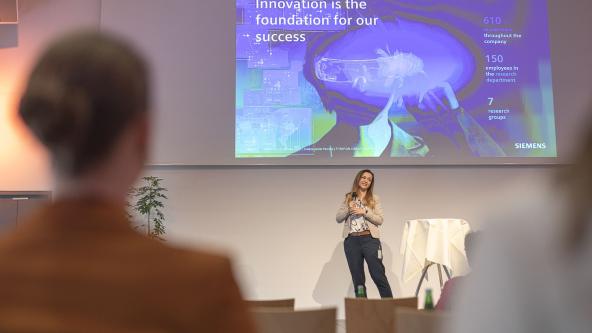
Österreich radelt zur Arbeit
Fit zum Job und Chance auf Preise sichern.
Empowered
People
People
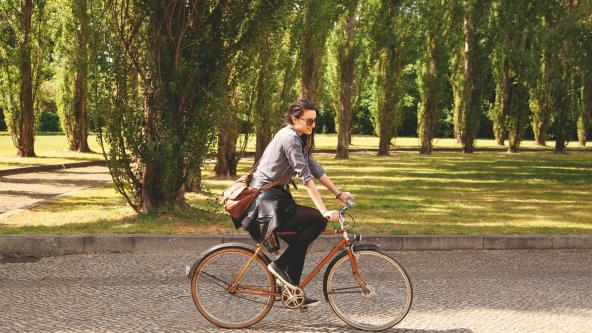
Umweltfreundliche Energieversorgung
Neue F-Gas-freie Mittelspannungsschaltanlage für die Energienetze Steiermark.
Umwelt &
Nachhaltigkeit
Nachhaltigkeit
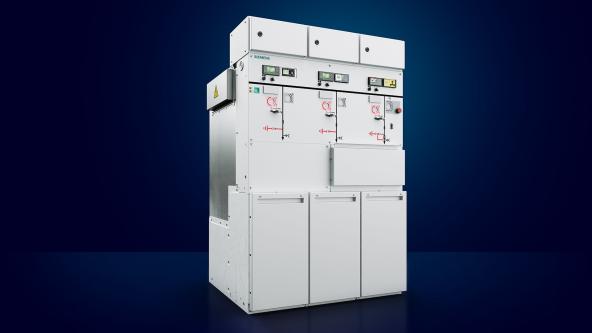
„Führung ist kollaborativer geworden“
CEO Patricia Neumann in der Tageszeitung "Die Presse".
Empowered
People
People

Wenn Glas immer grüner wird
Strategieplan der Stoelzle Glasgruppe für die Senkung des Energieverbrauchs um 20 Prozent und halber CO2-Ausstoß bis 2030
Umwelt &
Nachhaltigkeit
Nachhaltigkeit
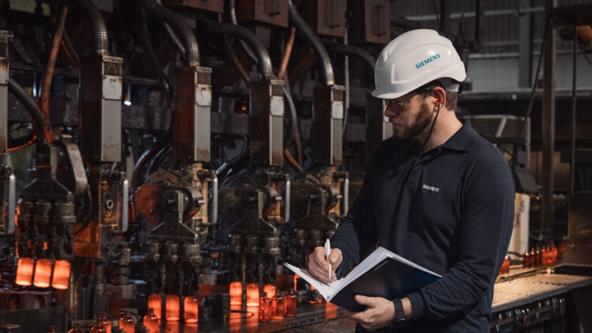
Partner von der Pike auf
Siemens als Gründungsmitglied beim Fest zum 50jährigen Bestehen des VSÖ.
Corporate
Citizenship
Citizenship
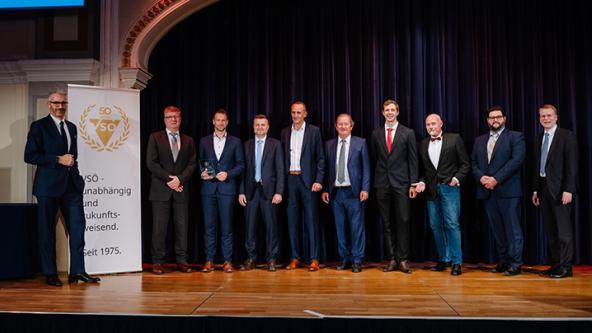
Auf den Flügeln des Erfolgs
WIKARUS: Österreich auf Platz 2 in der Kategorie "Unternehmen des Jahres" beim Salzburger Wirtschaftspreis.
Corporate
Citizenship
Citizenship
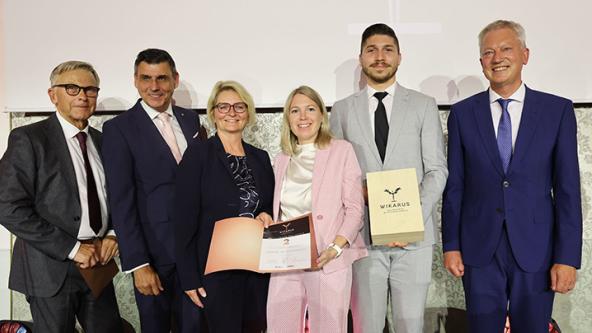
Produktion auf nächstem Level
„Accelerate your digital Transformation“: Siemens auf der SMART Automation 2025.
Digitale
Transformation
Transformation
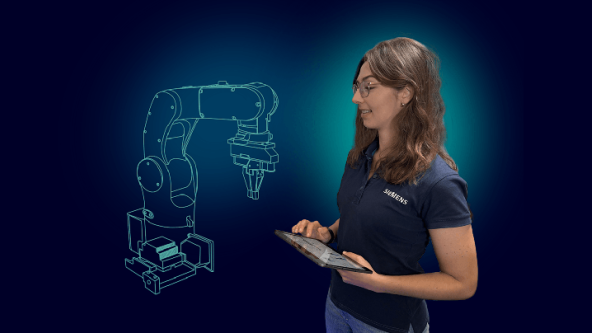